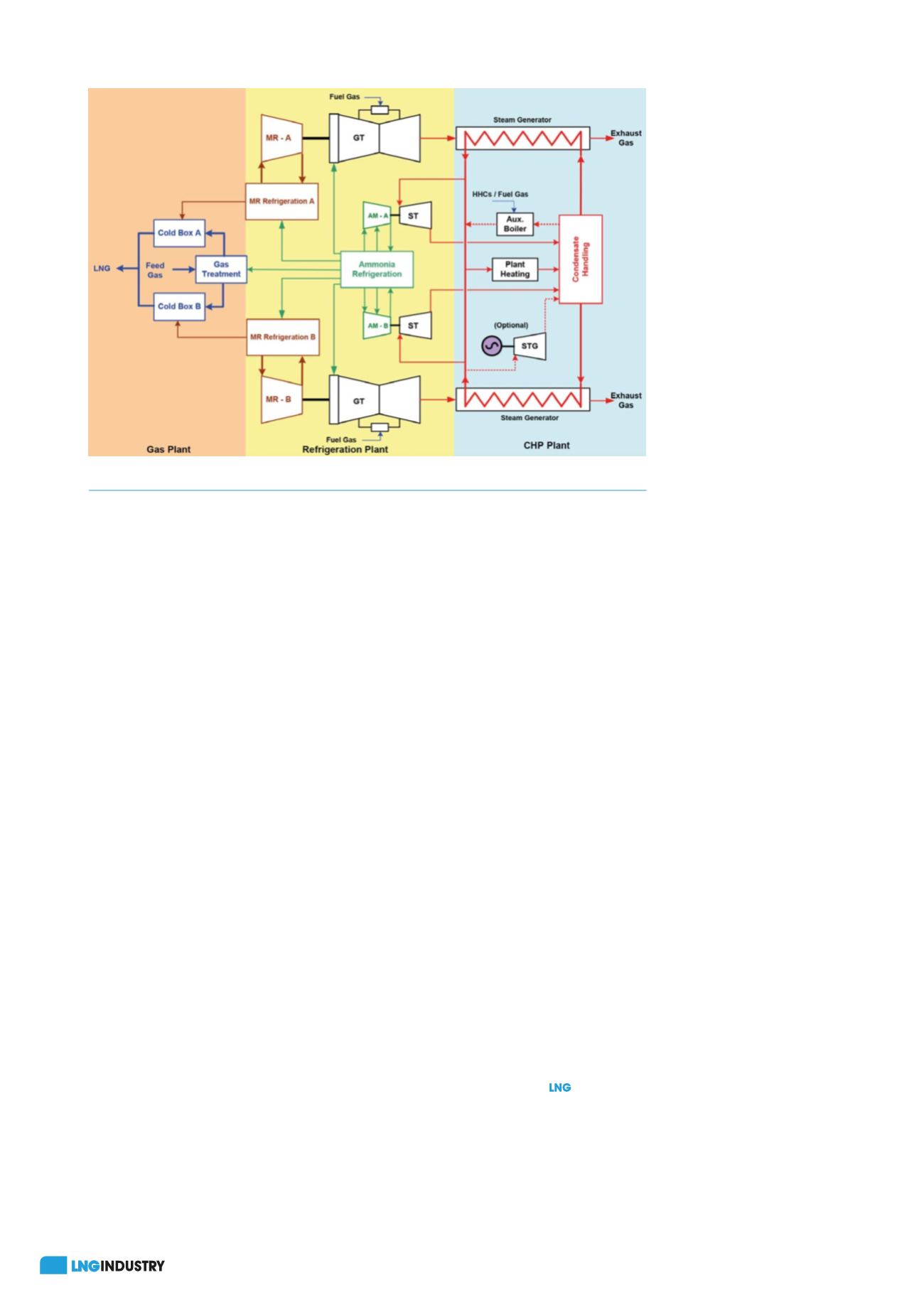
44
January 2020
selection of smaller, compact, efficient gas turbines and
smaller steam turbines in the OSMR process is aimed at
developing simple, compact, modular mid scale LNG trains
with a nominal capacity of 2.0 million tpy. Plant availability
and turndown is increased by selecting a two-in-one train
design, where two identical liquefaction circuits with separate
mixed refrigeration loops powered by individual gas turbines
are used in each OSMR LNG train. A single pressure level is
utilised for the steam system to minimise complexity for the
2.0 million tpy nominal capacity LNG trains. LNG projects are
developed with multiple LNG trains capable of operating
independently while sharing a few plant utilities among the
trains, such as power, water, air and nitrogen. OSMR
liquefaction train based plants are developed in a similar vein,
with the closed steam and condensate handling systems
within each of the trains to maintain independent train
designs with better modularisation, construction and
operation. An auxiliary boiler is used primarily as a plant
waste gas consumption boiler and to assist with steam unit
startup and balancing. The primary waste gas in the plant is
high N
2
vapour rejected from the BOG recovery unit.
Typically, LNG plants are developed with their own
dedicated power plant rather than relying on the local grid. But
when reliable grid power is available, imported electrical power
is an efficient option to meet auxiliary plant power
requirements. Plant power demand in an LNG plant fluctuates
with ship loading operations causing an increase in plant
power demand. In remote locations where LNG plants are built
with no access to an electrical grid, plant power can be
generated within the site using a steam turbine generator in an
OSMR Plant, as shown in Figure 2. This would reduce the
amount of steam available to drive the ammonia refrigeration
compressors, hence reducing liquefaction capacity and train
production compared to a plant with imported grid power.
When multiple trains are in a plant, sufficient reliability is
provided by the multiple steam turbine generators. Plant power
demand increases during ship loading operations are met by
utilising more fuel in the aux boilers to produce more steam for
the power generators.
The use of an island
mode combined cycle power
plant to support an
all-electric LNG facility has
been proposed for certain
projects to improve thermal
efficiency compared to a
typical open cycle industrial
gas turbine driven LNG plant.
The use of electric drives in
large refrigeration
compressors adds more
complexity to an LNG plant,
requiring variable speed
drives for the large motors
along with the management
of startup and shutdown
dynamics of these motors.
Furthermore, the size of the
combined cycle power plant
including spares required to
meet an adequate level of
redundancy for an LNG facility
is generally much larger, therefore resulting in higher overall
project costs. The overall efficiency of the facility decreases
during operations since the power plant generally operating at
60 – 70% of its capacity, including installed spares. Therefore,
the optimum design will utilise a combined cycle refiguration
configuration, such as in the OSMR design.
Key takeaways
There is increased scrutiny on carbon emissions throughout
the natural gas supply chain, from upstream flaring to LNG
plants and LNG shipping. LNG plants consume a significant
amount of power and typically use open cycle gas turbines.
The power industry has moved from open cycle power plants
to combined cycle power plants, starting in the 1960s with
combined cycle considered best practice for the industry.
The LNG industry has used open cycle gas turbines for
driving refrigeration compressors over several decades with
minimal consideration for efficiency or carbonbemissions.
The use of combined cycle power for direct driving the
refrigeration compressors provides significant energy
efficiency improvement to an LNG plant, and can reduce
fuel consumption and carbon emissions by nominally
20
–
25% compared to traditional open cycle LNG plants.
The additional cost of equipment associated with the steam
system is offset by improved efficiency of the plant due to
fuel gas savings and the extra revenue from the additional
LNG produced in the plant. Furthermore, with reduced carbon
emissions, combined cycle refrigerant LNG plants, such as
the OSMR-based LNG plant, will have a smaller carbon
footprint,benabling it to be utilised in carbon constrained
jurisdictions and maintain social licence as a best available
technology.b
References
1.
‘Tangguh LNG – Energy EfficiencyMeasures through Life Cycle
Cost Analysis’,
Gastech
, (2005)
2. ‘GHG Emissions fromLNG Systems – AQatar Perspective’,
IPIECANatural Gas LCAWorkshop
, (2012)
3. BALLING, L. and BAUMGARTNER, R., ‘Forty Years of Combined
Cycle Power Plants’,
ASME Power Division
, (2002)
Figure 2.
The two-in-one OSMR® LNG process schematic.