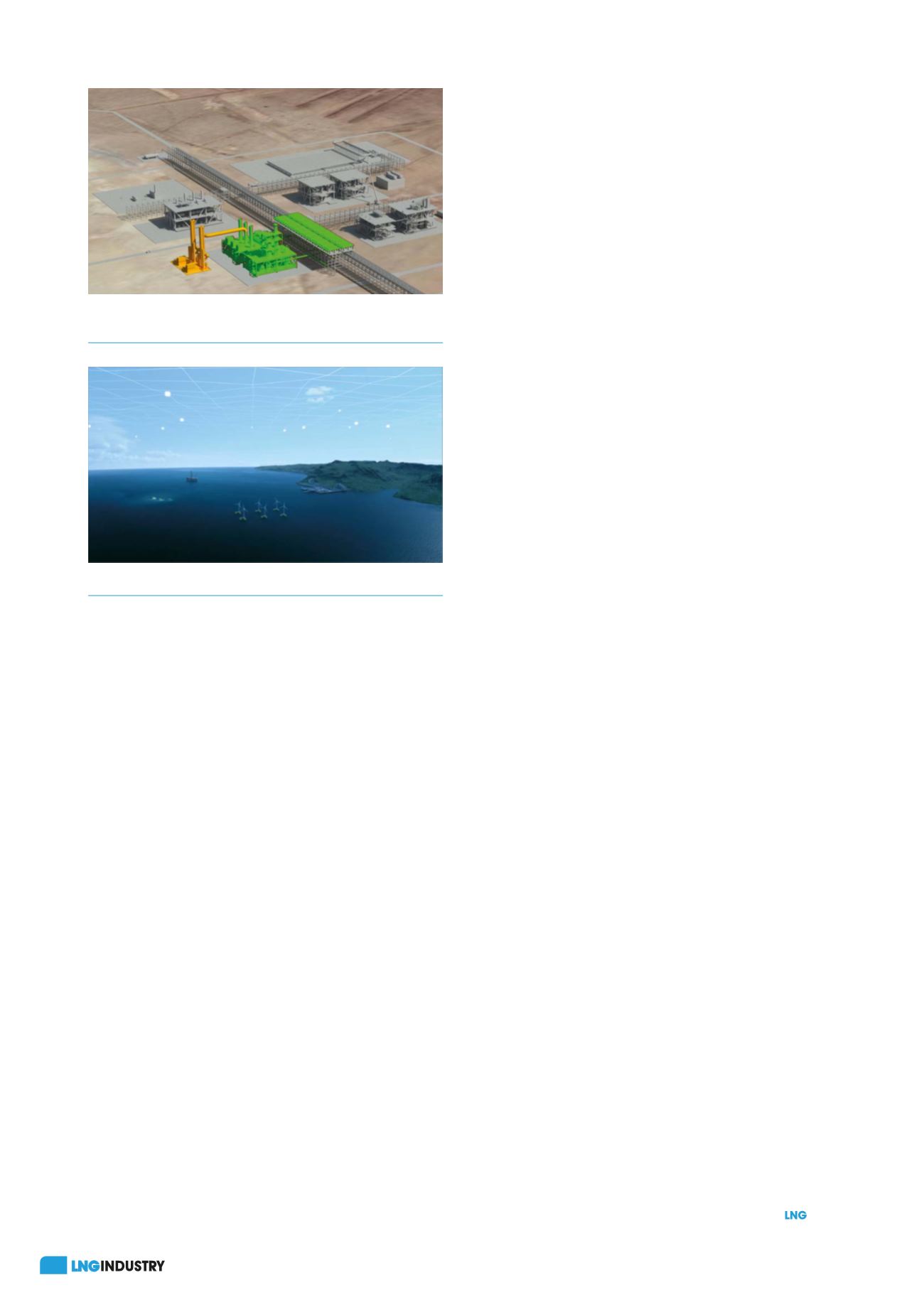
40
January 2020
gas easily achieves 0.16 tCO
2
e/tLNG with a carbon capture
efficiency of 80%. In this application, two containerised
Just Catch units are located on 50% slip stream of flue
gas as not all the flue gas needs to be treated in order to
meet the GHG emission specification. For carbon capture
to be a viable option, there needs to be a means of storing
or utilising the captured CO
2
as previously discussed.
Aker Solutions’ Just Catch is a standardised, modular carbon
capture unit with CO
2
capacities up to 100 000 tpy. A
100 000 tpy Just Catch unit, for example, can treat all the
flue gas from a single GE LM2500+G4. It can produce CO
2
at 99.95% purity at approximately 2.5 barg. The Just Catch
standardised design leads to rapid deployment with a
small footprint of 25 m by 18 m and only needs hook up to
heating medium and power with all other utilities included.
Incorporating Just Catch onto the refrigerant compressor
gas turbine drivers is a versatile and cost-effective way of
capturing CO
2
as not only is it containerised, but it also
utilises Aker Solutions’ proprietary amine. This is formulated
specifically for use in gas turbine exhaust gases with
significant advantages in terms of the environment and lack
of degradation over other amines available in the market.
Critical to carbon capture and also electrification
configurations being viable are the external factors of
availability of power import and the storage or export route
of CO
2
. It is highly likely that what is needed outside of the
facility fence dictates the configuration selected.
Electrification
Electrification is the most common configuration currently
being considered as a means of reducing CO
2
emissions. This
involves replacing the plant’s gas turbines with e-drives and
generating/importing electrical power.
Importing electrical power from a local grid as a
replacement for all power or just the auxiliary power is an
attractive option, especially when that power is generated by
renewable sources. For facilities with no available power
import, a combined cycle gas turbine (CCGT) plant
supplemented with renewable power from wind turbines or
solar panels could be an option.
For the relatively small auxiliary power plant of 45 MW,
just improving its efficiency by converting it to a CCGT or
employing higher efficiency turbines would not meet the
target emissions. Completely eliminating the auxiliary power
plant by importing auxiliary electrical power reduces the
associated GHG emissions to the target emissions if the power
import is from a low GHG emitting source, such as renewable
energy. Weighed against power import in the decision making
process is the availability of imported power as this may
impact the plant’s ability to meet production. For higher CO
2
feed gas, helper motors on the refrigerant compressors could
be utilised to compensate for this. In effect, this increases LNG
production with the fuel gas combusted remaining constant
since the electrical power is imported, and as a result GHG
emissions reduce per tonne of LNG.
Although eliminating the auxiliary power plant enables
us to meet the emissions target, further reductions could be
achieved by adopting a full e-drive solution where the
refrigerant compressor gas turbines are replaced with
e-drives and the electrical power imported from a lower
GHG emissions source. With 118 MW of refrigerant
compression, if all or part of this driver power can be shifted
to electrical power, increasing power import, then step
change reductions in CO
2
emissions are observed.
As this
case study configuration contains three aeroderivative
refrigerant compressor drivers, options exist to replace one,
two or all three of these.
A true e-drive solution where all
three aeroderivative refrigerant compressor drivers are
replaced with e-drives and power imported results in CO
2
emissions of 0.04 tCO
2
e/tLNG.
Key takeaways
Improving the efficiency and thereby increasing LNG
production for a determined refrigerant compressor
aeroderivative driver configuration has a positive impact
on GHG emissions. However, this alone is unlikely to reduce
emissions below 0.21 tCO
2
e/tLNG. Utilising power import
significantly reduces GHG emissions, but the fall depends
on the quantity of power available and is dependent on it
being from a renewable and reliable power source. Smaller
power imports could be used to replace or supplement the
auxiliary power plant, lowering emissions to 0.16 tCO
2
e/tLNG.
Further emissions (per tonne LNG) reductions could be
achieved by increasing power import and utilising this to
drive refrigerant compressor helper motors. Even more of a
reduction can be achieved by replacing the refrigerant gas
turbine drivers with electrical motors in conjunction with
importing more power. However, not all LNG projects will
have power import available. For these projects, carbon
capture on gas turbine flue gas is an option if the CO
2
can be
used as a saleable product, for re-injection or for EOR. Finally,
more efficient power generation on-site in conjunction with
an e-drive configuration could be used, with configuration
options including CCGT power plant supplemented with
renewable power from wind turbines or solar panels.
Figure 4.
Just Catch carbon capture technology on a
3.5 million tpy LNG train.
Figure 5.
Floating wind farms provide renewable power.