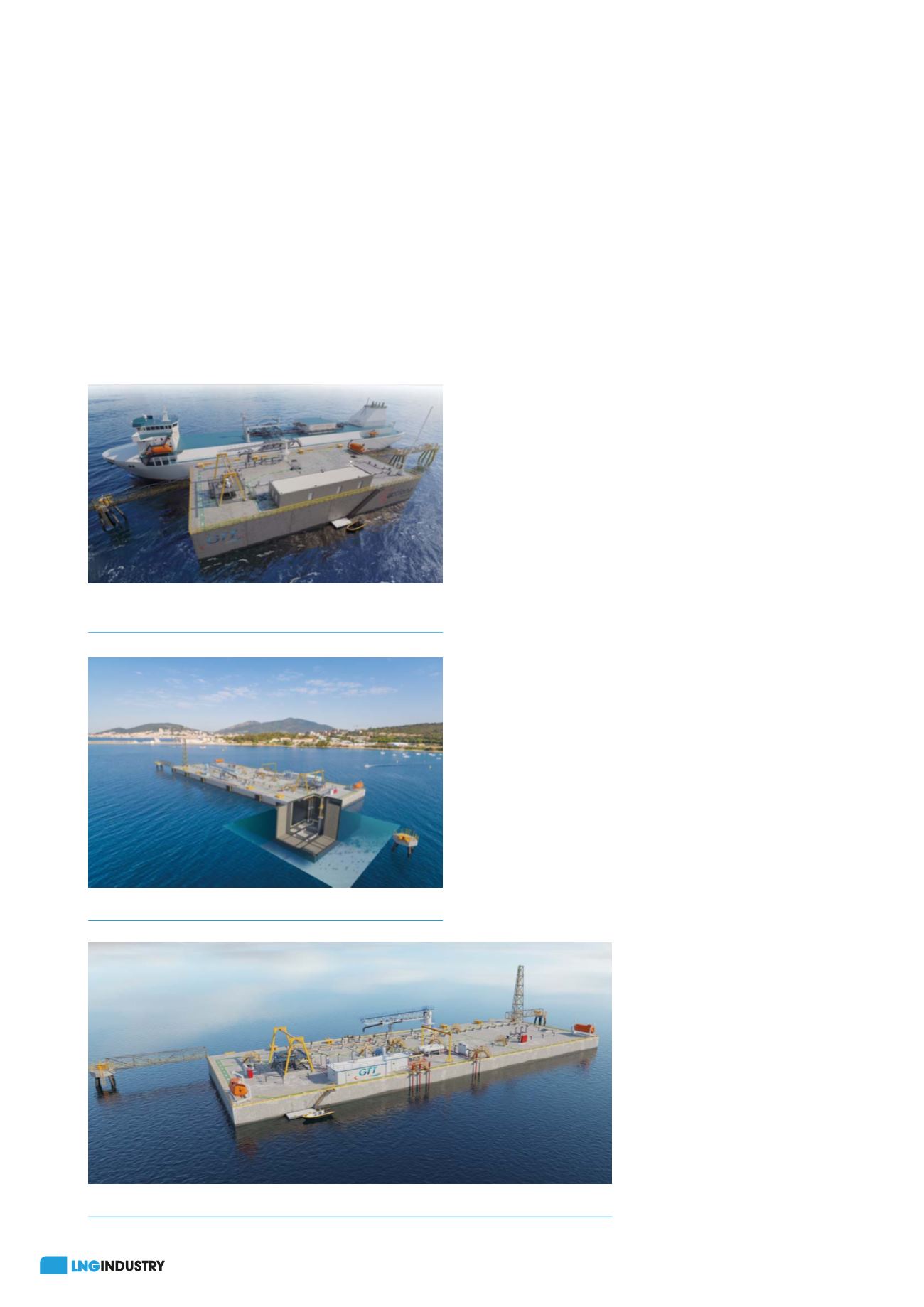
50
January 2020
liquefied gas containment tanks in floating or dry docks.
The finished facilities are then towed to the installation
location, where they are ballasted to rest on the seabed. A
GBS can be installed in a harbour or in a remote area, with
very limited requirements for any additional infrastructure.
The selection of GBS technology for building offshore oil
and production facilities in the North Sea led the LNG
industry to consider the application of this technology for
LNG.
Structural simplicity
The primary components of a GBS include: an integral outer
concrete tank; a moisture barrier to prevent water migration
from the concrete to the insulation; an insulating structure
fastened to the concrete wall, base and tank roof; and a
corrugated membrane welded onto the insulating panels
of the wall, base and tank roof. The general architecture of
the GBS is designed to provide a massive, rigid structure – a
fundamental requirement for LNG storage.
A flexible solution
A GBS is suitable for various liquefied gas applications,
including LNG, ethane, LPG, etc. It is appropriate for storage
capacities from 5000 m³ to 200 000 m³ or greater (several
caissons can be combined to increase storage capacity).
In addition to this, all types of vessels (small LNG tankers,
containerships, ferries, etc.) can moor alongside it.
A GBS can contribute to the LNG supply chain in the
form of a liquefaction or regasification plant, peak shaving
storage, or a satellite station. It can also be utilised in inland
distribution systems. In a harbour setting, this type of
storage can also be used for bunkering vessels with LNG as
fuel. Another option for GBS utilisation is power generation
(e.g. captive power, etc.). Indeed, for small and medium-sized
power plants, GBS technology can be connected to a
regasification module and replace the LNG floating storage
and regasification unit (FSRU) with a solution that requires
no onshore space, thus providing significant cost savings.
Reliability and safety combined
GBS technology combines the structural resistance of
concrete with the insulation performance and tightness
of membrane containment. In order to achieve this, the
structure incorporates Gaztransport & Technigaz’s (GTT)
membrane containment system, with the possibility of
using various GTT technologies, such as: Mark III, GST® or
GTT MARS™ (for LPG applications).
This type of structure is highly durable and built with
maintenance-free material. A GBS benefits from high
resistance to extreme environmental conditions, making it
suitable for both harsh and arctic environments (such as ice
and earthquake zones). In addition to this, industrial risk is
considerably reduced, since the equipment is located far
from populated areas. As the storage is under atmospheric
pressure, the explosion risk is limited, which provides a high
level of safety.
As far as the protection of the storage tank is
concerned, in contrast to onshore storage, a storage tank on
a GBS may be exposed to vessel impact. However, even if
high-speed collisions cause significant local damage to the
caisson base structure, this will
not result in loss of containment
and the risk of LNG spillage.
Again, the separation of the
functions guarantees the integrity
of the storage tank even in the
event of severe impact. Indeed,
the tank is located in the middle
of the caisson base, several
metres inside its outer walls. In
the event of collision, it is the
caisson base structure that is
impacted and structurally
affected, not the storage tank
structure.
In addition to the fact that the
structure is able to withstand
Figure 2.
An internal view of a GBS.
Figure 3.
An aerial view of a GBS.
Figure 1.
Acciona gravity-based structure (GBS) LNG storage
concept.