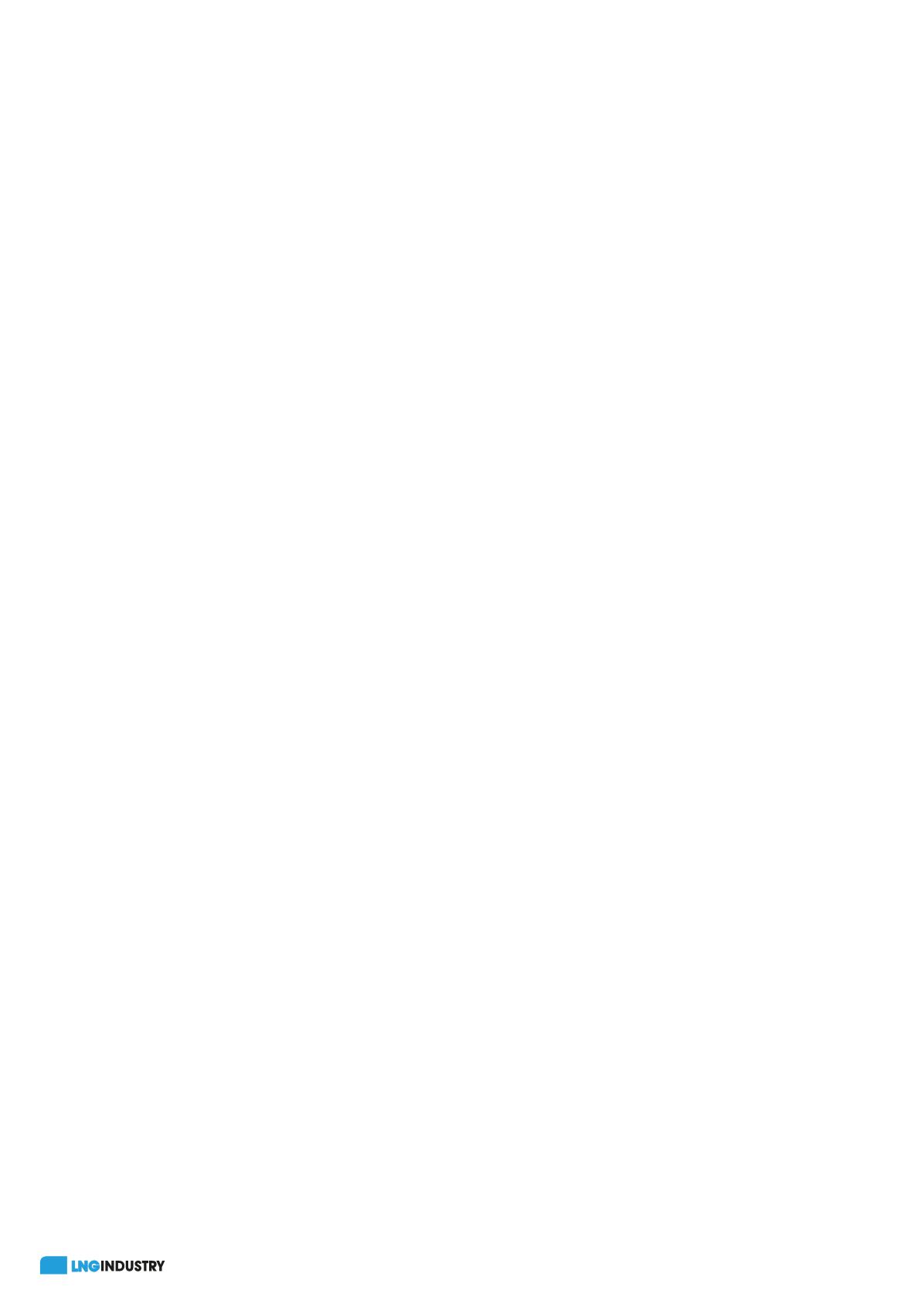
54
January 2020
Propulsion system choices
Propulsion system design has evolved to a position of
dominance for two-stroke engines of which there are two main
types: MAN Energy Solutions’ ME-GI high pressure gas injection
system, and Win-GD’s X-DF lower pressure system. These two
designs have made up the vast majority of new orders in the
last 12 – 18 months, with a slight preference for the X-DF
system which is making up market share against a higher
installed base of ME-GI units. Despite the strong competition
between the two providers, the differences between the
systems mean they both have pros and cons.
It is agreed that MAN’s ME-GI engine technology offers a
higher level of efficiency and operational flexibility, and is less
sensitive to fuel quality. It also has little or no methane slip
– where unburnt methane is present in the exhaust – which is
more common in the XD-F system. Considered a contribution to
greenhouse gas emissions, methane slip is not currently subject
to regulation, but there is increasing discussion suggesting it
might be in future. The major consideration in the ME-GI
system is that its gas injection system operates at high pressure
of 300 bar. While the engine itself is robust and reliable, owners
need to have a similar level of confidence in the high pressure
fuel gas supply units. In addition to the high CAPEX required for
the engine, the fuel gas supply system is also expensive.
Indeed, one compressor can cost as much as US$5 million – not
far off the cost of the engine itself – and, for redundancy, often
two compressors are provided.
The major advantage of the XD-F is the much lower
pressure at which the gas is injected – approximately 20 bar –
which contributes to reducing the CAPEX on the fuel gas supply
system and increases reliability. However, due to its different
operating principles, the efficiency of the X-DF is lower than the
MEGI with higher risk of ‘knocking’ and more sensitivity to fuel
quality and methane number in particular. If this is too low, the
engine may have to be de-rated and will be unable to operate
at maximum power. The X-DF is less flexible in responding to
load changes such as when the ship sails in rough weather and
may struggle to keep required load on the engine in gas mode
alone. WinGD has developed a dynamic combustion system
which improves the ability of the engine to cope with load
changes, increasing supply of diesel oil when load conditions
change. This means the engine is not as efficient in heavy
weather conditions as it would be in normal conditions. Despite
these challenges, the popularity of the X-DF can be ascribed
both to a slight CAPEX advantage, and also a potential
advantage in terms of emissions compliance with IMO NO
x
Tier III regulations when burning gas.
Until now, LNG carriers have tended to achieve Tier III
compliance in Emission Control Areas (ECAs) with liquid fuel.
This provides operational flexibility because vessels loading
cargo in an ECA would have no gas onboard to use as fuel.
Using low sulfur fuel means that the vessel would also need
selective catalytic reduction (SCR) technology to be fitted, in
order to achieve NO
x
Tier III compliance. An argument made by
Win-GD is that permanently using gas as fuel negates the need
for that additional expense.
Containment excitement
The second area of focus for LNG designers is in the choice
of cargo containment system (CCS). Recently, the decision
regarding which CCS to utilise has been significantly influenced
by the steady evolution in performance of these systems in
terms of boil-off gas (BOG). This is a process that has taken
place over the last five years or more, when boil off rate
(BOR) levels could be as much as 0.15% per day. The latest
developments in membrane systems have brought this number
down to 0.85%, or in the case of the latest GTT Mk III Flex+, a
BOR of 0.07%.
There has been a similar trend in Moss and SPB designs
where the BOR has been brought down to the region of 0.8%,
driven by the fact that propulsion systems have become so
much more efficient compared to the previous steam and
dual-fuel diesel electric engines, so there is less need to
manage the BOG by burning or reliquefying it.
The choice of CCS continues to be a function of the
shipyard selected by the owner. Construction at
Samsung Heavy Industries will mean installing GTT’s Mk III,
while DSME offers GTT’s NO96. At Mitsubishi Heavy Industries,
carriers will be installed with Moss-type containment. The
principal exception may become China’s Hudong, which has
traditionally offered GTT’s NO96, but is now working on designs
with GTT Mk III containment.
New CCS designs have also been developed. For example,
Japan Marine United is in the process of delivering a new
generation of LNG carriers with SPB tanks, but in general the
market seems content with the choices on offer. Of
conventional membrane systems, GTT is working on a new
system which it calls the NO96 Flex. This system will
essentially combine its Mk III and NO96 systems into one, with
commercial availability expected by 2021.
Adding a reliquefaction plant
The trend towards lower levels of BOR has prompted increased
interest in the installation of reliquefaction capacity onboard
vessels, reflecting the desire to manage BOG for commercial
reasons. Reliquefaction capacity is now common both for NO96
and Mark III containment designs, and certain shipyards also
offer partial reliquefaction systems which can be employed in
combination with a modern CCS, using either a high pressure
gas compressor for ME-GI engines, or a booster compressor
for X-DF systems. Using a reliquefaction system capable of
reliquefying all or just part of the natural boil-off enables ships
to slow steam when required, without wasting excess BOG.
While a previous generation LNG carrier might have the
capacity to consume close to 200 tpd of BOG, in order to reduce
pressure on the CCS, the efficiency of modern engines now
means this is no longer possible as the engine would typically
consume less than 100 tpd. The reliquefaction plant can
therefore be used to handle any additional cargo not used in
the engine or generators.
The installation of a reliquefaction plant allows an operator
to make choices regarding fuel usage, and to operate at slower
speeds to fit arrival schedules without having to burn the gas
in a gas combustion unit. It also suits modern trading patterns
where ships take ‘reloads’ as cargo, loading cargo from receiving
terminals rather than dedicated export facilities. This also
creates extra capacity to cool down the cargo enough to be
loaded, since gas at a receiving terminal is normally stored
warmer than at an export terminal.
Stable vessel sizes set to grow?
After a period in which yards and designers increasingly
pushed the envelope in terms of LNG carrier capacity, the
LNG market appears to have settled for now on ships sized