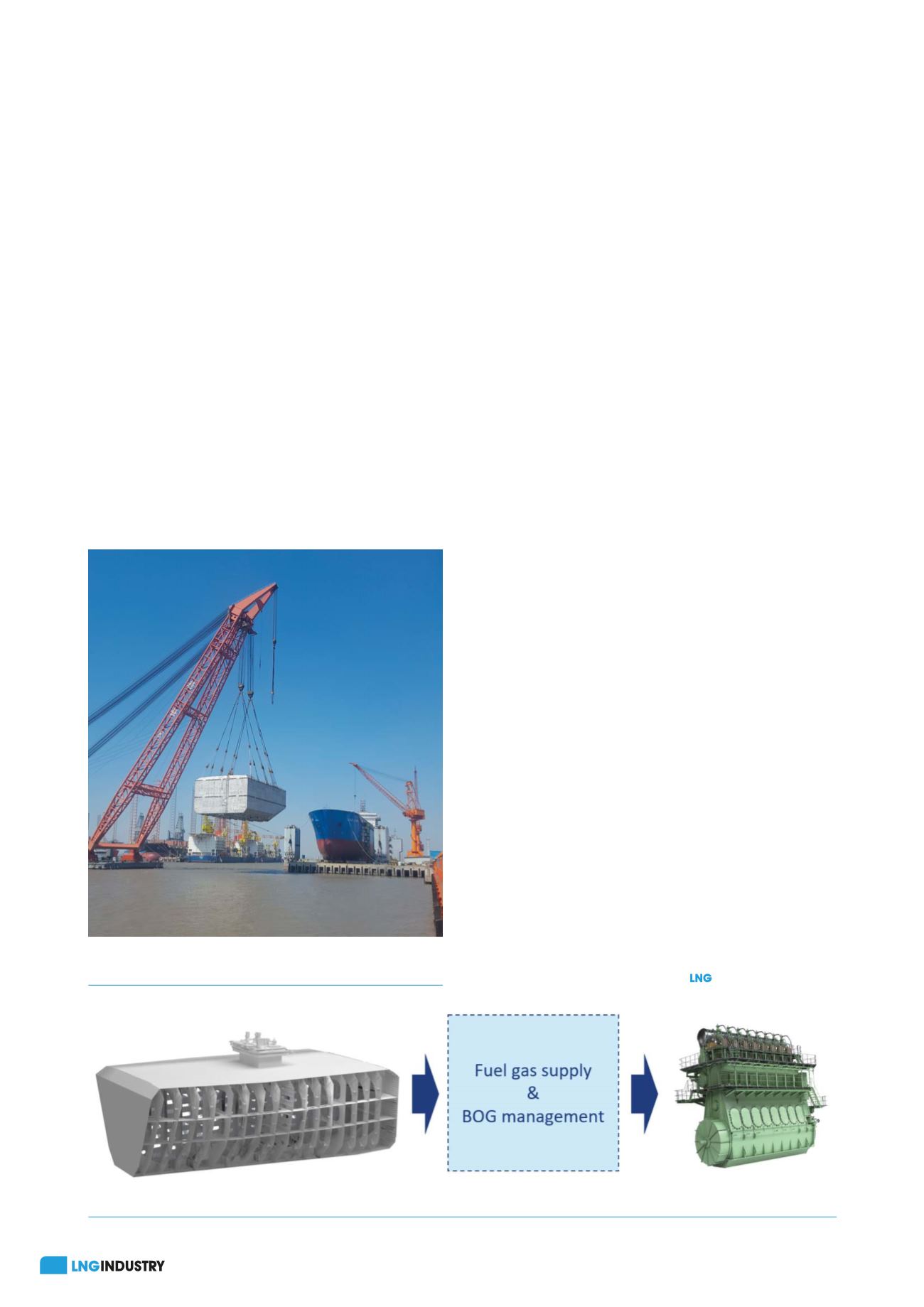
48
January 2020
the flexible seal between each panel due to hull deflections.
The density of the polyurethane foam is selected for its
best possible insulating properties, i.e. a density of around
40 kg/m³. The tank is constructed outside the ship and
is lifted into the insulated tank space with integrated
hardwood tank supports.
Low boil-off rate
The arrangement with insulated tank space and
non-insulated tank space provides an access space in
between the tank and the secondary barrier insulation. The
access space is an important feature for lifelong quality
control of the LNG barriers, with easy access to any part
during drydocking.
Probably less evident is the insulating function of the
access space. The access space is filled with dry nitrogen.
The LNG tank is thus encapsulated by a volume of cold
nitrogen gas with the secondary barrier insulation on the
outside of the nitrogen volume. The access space is cooled
close to cargo temperature before operation and maintained
at this temperature.
Nitrogen gas’ insulating properties improve by a factor of
2.5 times when cooled from 20°C to -160°C. The access
space volume will therefore act as an effective heat transfer
break between the tank shell and the insulation, i.e.
increasing the total insulation performance. Together with
the low-density polyurethane foam panels, this produces less
boil-off gas (BOG) compared to the traditional arrangement,
which utilises an insulated tank in an ambient temperature
hold space.
LNT Marine is considering several options to utilise the
access space for further reducing BOG. With gas engines
becoming increasingly efficient and pumps supplying fuel to
the engines, the lowest possible boil-off rate (BOR) is always
an aim.
LNG fuel gas operation
The present demand for marine LNG fuel technology
contrasts with the available ships that are equipped with
Type C vacuum insulated LNG fuel tanks. When these ships
were designed, BOG was of no concern and gas supply
pressure was achieved with a simple heat exchanger
pressure build-up unit.
In the present transition from fuel oil to LNG fuel, factors
such as fuel volume, pressure build-up time, ramp-up speed,
bunkering speed, temperature restrictions for bunkering and
tank pressure variation during operation, are all of concern
to a ship operator. Fuel gas supply systems and boil-off
handling systems are increasingly being optimised for
individual ships’ operating requirements.
LNG fuel operation is something new and different from
oil fuel systems. A lot is being done to offer simple operation
LNG fuel systems to enable the smoothest possible
transition from fuel oil to LNG fuel.
Conclusion
By increasing the maximum vapour pressure for prismatic
tanks from 0.7 to 2.0 barg, an important design basis has
been achieved, particularly for large and volume sensitive
LNG fuel tank installation.
Fuel supply and boil-off handling systems can be
simplified. A holding time requirement of 15 days is far
easier to fulfil. Boil-off compressors plants in regulation with
LNG fuel pumps as fuel gas supply system may be replaced
by fuel pumps only. The need for boil-off compressors for
boil-off removal from the tank may be replaced by tank
pressure build-up and possibly combined with compact LNG
subcooler units.
All in all, there is potential for a much simpler operation
than what is currently required of standard prismatic tanks.
It could be concluded that, with the introduction of novelly
designed LNG tanks, a milestone has been achieved in the
transition from oil fuel to LNG fuel.
Figure 4.
LNT Fuel-Box – the tank is constructed in parallel
with secondary barrier installation.
Figure 5.
Boil-off gas (BOG) management is simpler with increased pressure.