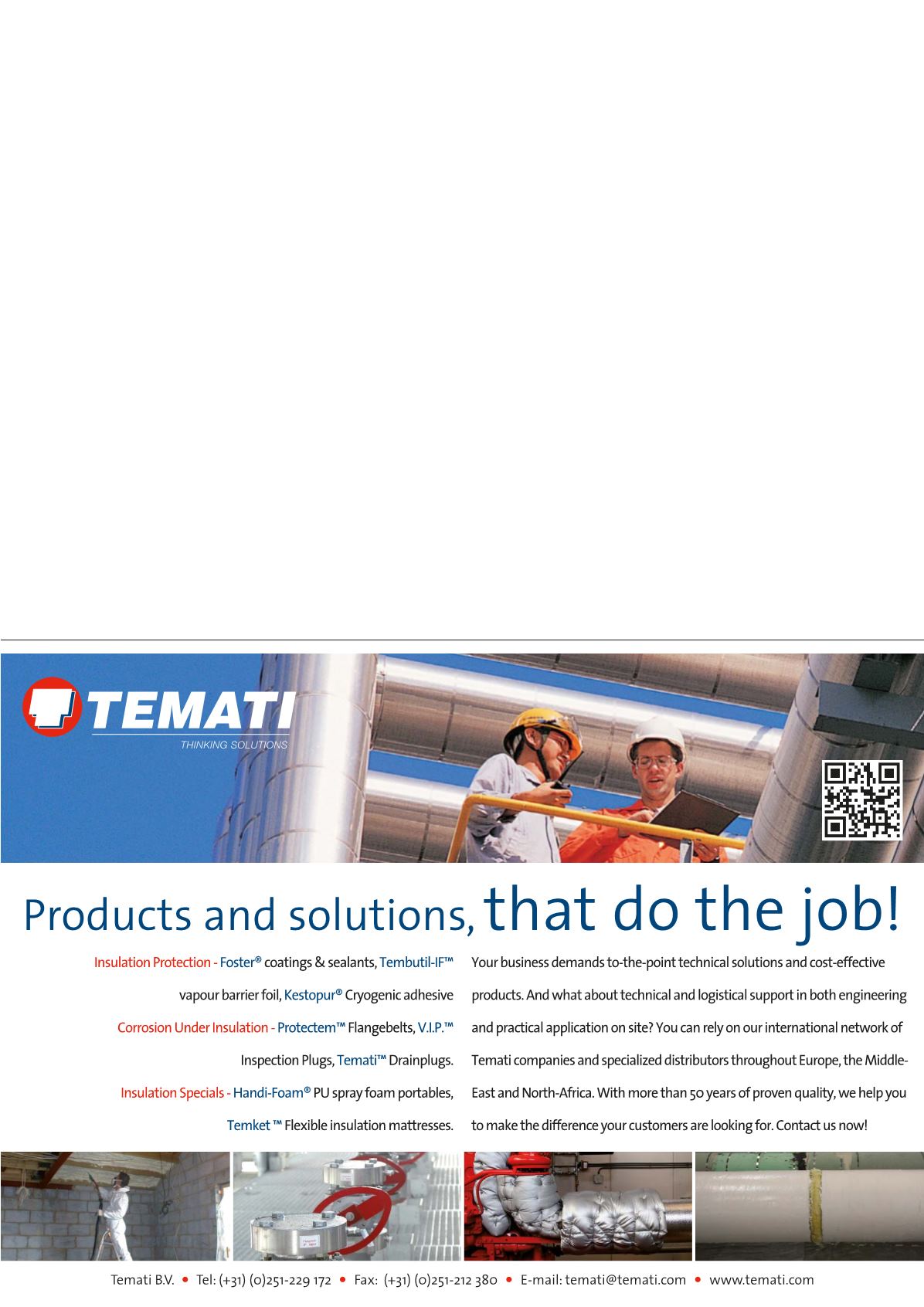
There are very high level safety regulations applied to
LNG containment systems based on limit state design.
LNT Marine has opted to utilise a full secondary barrier
outside the LNG tank in order to comply with the
regulations. The principle is taken from the IMO Type A tank
design, and LNT Marine has recently completed a ship
project in China, based on its LNT A-Box containment system,
which features a Type A tank.
Increased safety by two
independent LNG barriers
Full secondary barrier is designed as an integrated part of
the thermal insulation and is completely independent of the
tank itself. In other words, a failure in the tank will not affect
the secondary barrier or vice versa. In the unlikely event of
a tank leak, the LNG inside the tank will be collected in the
secondary barrier.
LNT Marine’s strategy was to develop a self-supporting,
novelly designed tank able to cope with a pressure of 2 barg.
During this process, an important aim of the company has
been that a standard quality workshop should be able to
construct the tank, rather than having to depend on
specialised workshops.
The company chose a design philosophy that is based on
complete independence between the two LNG barriers, or in
the terms in the IGC Code, LNT Marine has chosen the Type A
tank method rather than the Type B tank method.
Prismatic shapes, with distinct stress concentrations
and increased safety factors due to higher pressure, would
be demanding to deliver without considering the added
safety offered by a full secondary barrier. This is mainly
related to weld finish. LNT Marine considered that the
extremely high requirements of the welds would make a
tank without full secondary barrier tanks too expensive. The
estimated number of workhours to finish off the weld were
also estimated to be outside of what is possible within
normal commercial frames, and there is a risk to consider
when it comes to construction time. LNT Marine claims,
however, that the cost of secondary barrier per square
metre is no more than the cost of insulation for Type B
tanks. The full secondary barrier construction eases the
safety considerations associated with the tank construction
because it forms an essential part of the containment
integrity.
Separate activities during
construction
The full secondary barrier is installed separately inside the
ship tank space and is integrated into the tank supports
as one common secondary barrier surface. There are
polyurethane panels embraced by plywood and crack
arresting cloth, with a reinforced aluminium seal between
the panels. The tank supports are integrated with the panels
in the same manner as the panels are integrated with each
other, all in a way that prevents global forces acting on the
secondary barrier surface. As a result of the independence
between the barriers, the secondary barrier is not exposed to
any impact loads during operation, only minor movement in