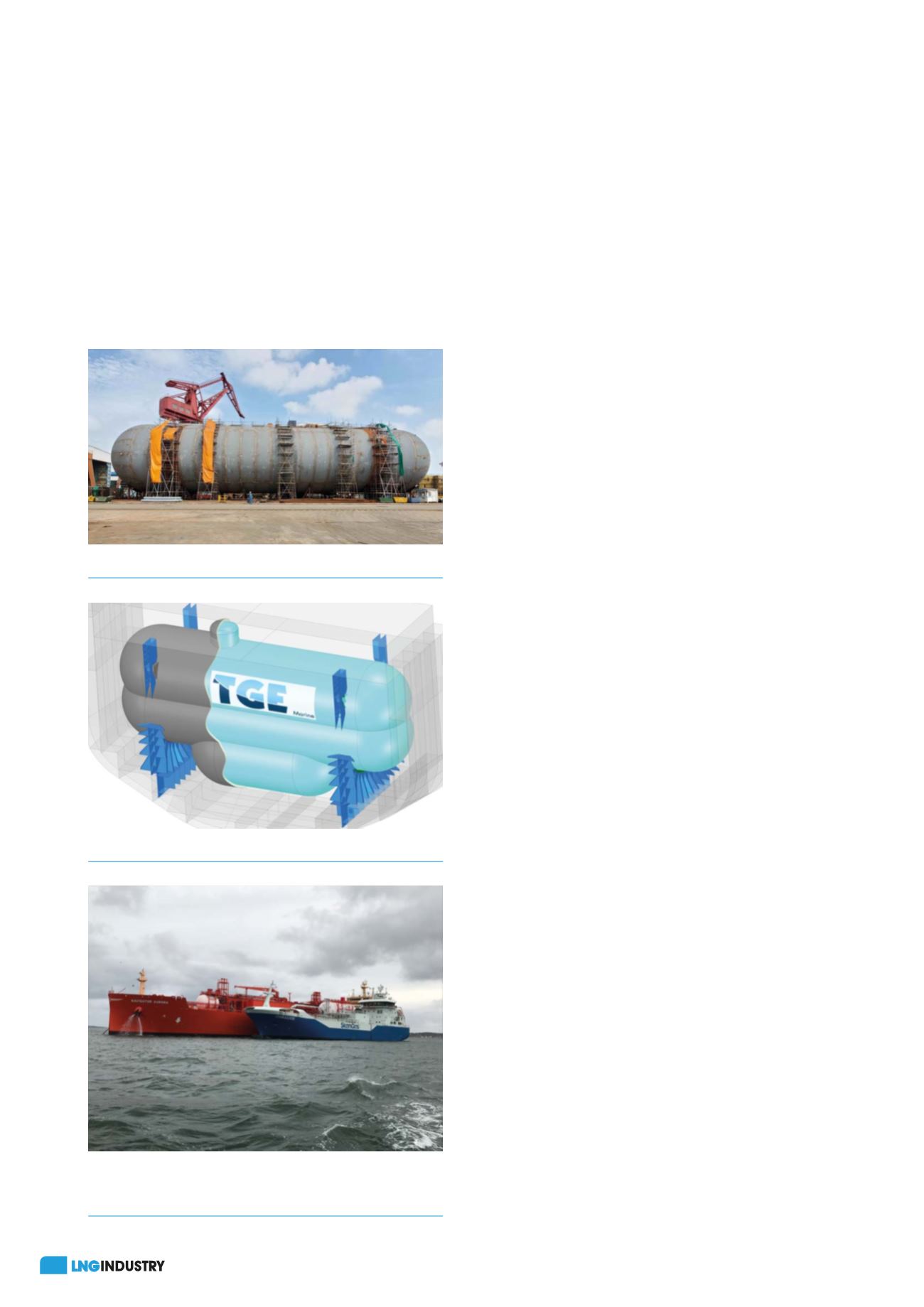
18
January 2020
Long established in the LPG and
ethylene trade
During the early days of marine liquefied gas trades, it
became clear that, for small and medium sized gas carriers,
pressure vessel type containment systems are the most
economic system. Obviously, for fully pressurised LPG
carriers, transportation at ambient temperatures requires
the gas to be transported at up to 18 bar pressure. With
the increase in tank size in the handysize segment, due
to economics for the tanks and trading requirements, a
reliquefaction plant is added and the design pressure is
reduced to 3 – 6 barg. For LPG, this leads to a breakeven
between semi-refrigerated carriers with pressure vessel
Type C tanks and fully refrigerated carriers with atmospheric
Type A tanks at approximately 22 000
–
23 000 m³ total tank
volume.
Most economic solution for
small scale LNG and LNG as fuel
For large LNG vessels of 150 000
–
210 000 m³, the most
established tank types are membrane and Moss type tanks.
A noticable market for smaller LNG carriers only developed
during the last decade. During the last decade, growth in
the small scale LNG trade and the arrival of LNG as fuel
have lead to a significant growth of the small scale LNG
fleet of vessels of 30 000 m³ capacity and below. In 2010,
a fleet of merely 13 vessels was mainly controlled by Asian
interests. By 2020, the fleet size will have been quadrupled
to more than 40 vessels. A strong factor in the growth of
the fleet are the LNG bunker vessels, which form the basis
of a worldwide LNG fuel infrastructure. Over 85% of these
newbuilds built between 2010 and 2020 are equipped with
Type C tanks. The technical superiority, as well as economic
considerations, form the basis of the domination of this
tank type.
Advantages of Type C tanks
From a design and project execution standpoint, the
benefits are as follows: Type C tanks have been established
under the IGC Code since the early days, with a design that
is considered inherently safe. Due to this safe design, a
secondary barrier is not required as no leakage can occur
over the lifetime of the vessel. The hold space around
the tanks is considered a gas safe area. With decades
of operation, this approach has proven to be a safe and
reliable design. The fact that there is no secondary barrier
needed is obviously also favourable to the economic
comparison to other tank types, such as Type A and
membrane type tanks. From a project execution point of
view, the main benefit is that the tanks can be completely
fabricated, insulated, tested and calibrated outside of the
hull. This decouples the tank fabrication schedule from
the building schedule of the vessel, and saves valuable
docktime. TGE Marine has even transported its Type C
tanks from the fabrication site in China to building sites
in Europe. For some more recent projects, as well as for
fuel gas projects, the tanks have also been delivered
fully outfitted to reduce outfitting time at the yard. With
TGE Marine’s expertise, small LNG carriers and bunker
vessels can even been placed at yards with little prior
references in the small scale LNG market.
Good examples are the
Coral Methane
(built in 2009) or the
first three newbuild bunker vessels (
Cardissa
,
Coralius
and
ENGIE Zeebrugge
).
Early adaption from ethylene to
LNG
On the technological side, the adaption of Type C tanks
from the previous application of LPG and ethylene to LNG
required some modifications in terms of both material and
design. LPG is usually transported at -48°C and ethylene
at -104°C, while LNG is transported at -163°C. This means
that instead of steel grades with nickel contents between
0.5% and 5%, for LNG, 9% nickel steel or stainless steel
has to be applied. Due to the low temperature, shrinkage
Figure 1.
Largest cylinder Type C LNG tank (14 000 m3).
Figure 2.
Trilobe Type C tank for container vessel retrofit.
Figure 3.
Type C tanks in various applications
–
35 000 m3 ethane transport, 2000 m³ LNG fuel, and 5800 m³
LNG bunker.