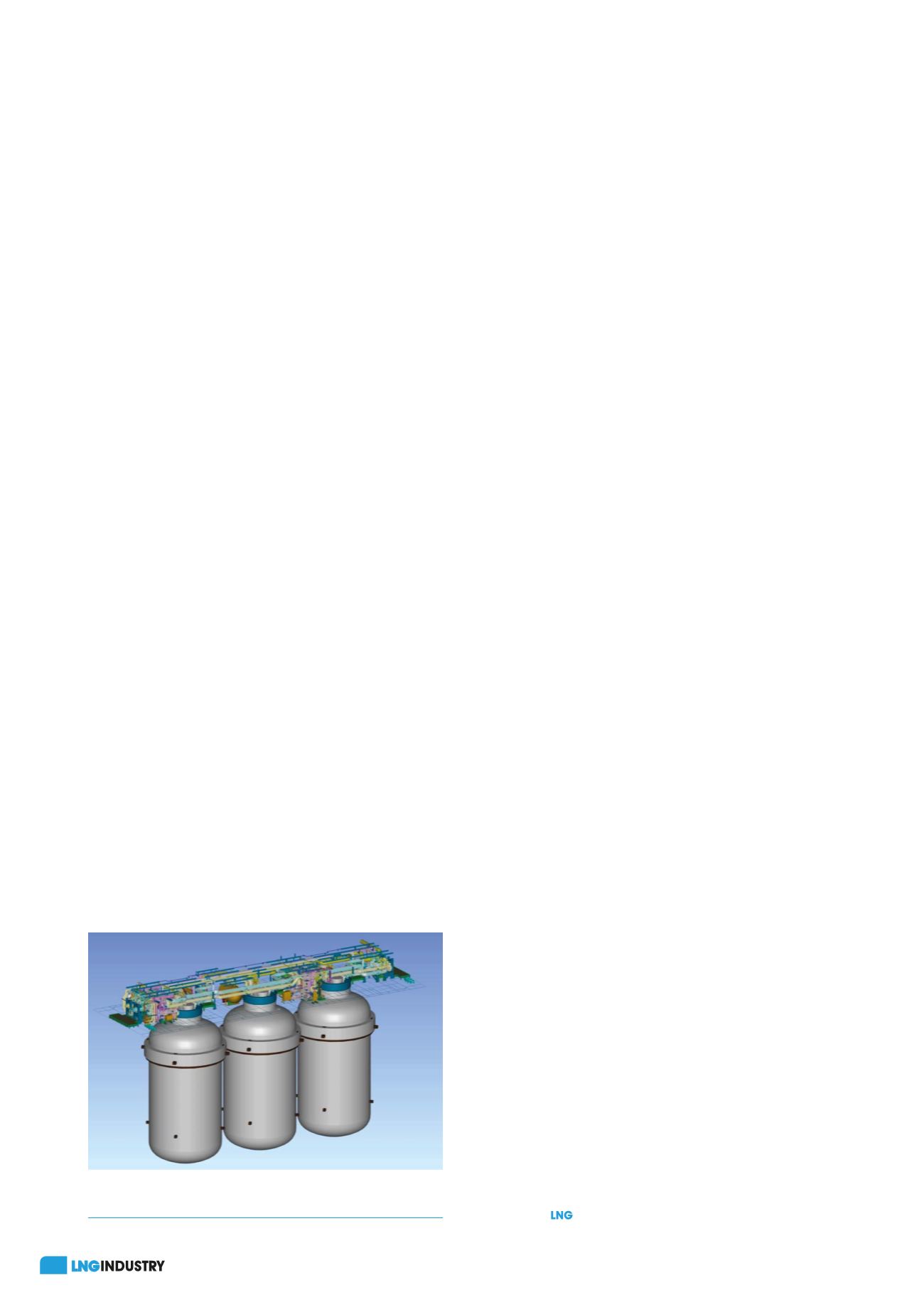
20
January 2020
becomes an issue, which has to be reflected in the design
of the tank shell and tank supports, as well as the design
of the insulation and the connecting piping. Depending on
the tank diameter, the tank will see a shrinkage in height
of up 40 mm. With this shrinkage, the diameter of the tank
will also shrink between warm conditions and cold loading
conditions. The design of the supports, therefore, will have
to consider that the tanks will shrink ‘out of’ the support
during operation. For bilobe type tanks, this phenomenon
is intensified in the knuckle between the two tank halves.
For the early designs of the bilobe type LNG Type C tanks,
TGE Marine has applied a patented design, which moves
the interface between the hull and the tank from the
circumference of the tank into the horizontal plane of the
support. The application of this patent will ensure longevity
of the support, wooden blocks and insulation over the
lifetime of the vessel.
Type C tanks in the FSRU market
The development of Type C tanks has not stopped with
their application to the small scale fleet. Two other areas
of application are the small scale LNG floating storage and
regasification unit (FSRU) market, as well as the LNG fuel
gas market. In the FSRU market, regasification barges can
be equipped with Type C tanks as storage, either sized for
small scale LNG parcels, or to increase the storage volume
in combination with a floating storage unit (FSU). Usually,
older LNG carriers are used as FSUs, but because they are
smaller in volume than modern LNG carriers, they would
not be able to complete parcels out of the supply chain as
a standalone solution. This can be achieved in combination
with added storage on the regasification barge. For this
application, the largest ever cylindrical LNG Type C tank
was recently fabricated by TGE Marine. The volume of this
tank is 14 000 m³, with a length of 74 m and a diameter
of 16 m. Type C tanks have generally increased in volume,
and the boundaries been pushed further by the newly
established ethane trade out of the US to Europe or Asia
calling for a new segment of large or very large ethane
carriers (VLECs). For large ethane carriers with a storage
capacity of 35 000 – 37 000 m³, the largest bilobe Type C
tanks with 12 000 m³ of single tank capacity have been
delivered. One particular design of the delivered VLECs
with a total capacity 84 000 m³ is equipped with trilobe
type tank design.
Application for LNG fuel
As stated above, size is not an issue for Type C tanks.
However, in the smaller range, volume efficiency and
therefore shape become the main challange. This smaller
range of Type C tanks with volumes of 300
–
3000 m³ has
found a new market in the application as LNG fuel tanks.
Here the tanks are used to store LNG as fuel on merchant
vessels of any kind. These can be cruise vessels, container
vessels, bulk carriers, car carriers, or any other type of vessel.
For this reason, Type C tanks have been integrated in the
IGF Code as one possible solution for fuel gas storage.
From a size of 300 m³, conventional insulated Type C tanks
are the most economical solution compared to vacuum
insulated tanks. Vacuum insulated tanks are further limited
in size and shape. While for a ship type with sufficient deck
space, conventional cylindrical tanks are used, this becomes
difficult for container vessels (for example), where lost space
is equivalent to loss in cargo capacity.
Trilobe shapes and vertical
arrangment
For the conversion of the 1000 TEU container vessel
Wes Amelie
, a solution could be found with the installation
of the cylindrical fuel tanks in the forecastle, minimising
the loss in cargo space. For a 1400 TEU vessel, however,
TGE Marine took a more innovative approach. The three fuel
tanks on this vessel were installed in a vertical arrangement
suspended into a fold space, essentially representing one
container bay in the hull, and supported by a ring type
support. The upper ring type support is used to keep the
stresses on the topside piping connections to a minimum.
The tanks experience the main part of the shrinkage below
the ring type support. The same concept has been used
for the eight vertical Type C tanks used as fuel tanks on
Heerema’s crane platform,
Sleipnir
. The volume of each
fuel tank amounts to 1100 m³, providing a total capacity of
approximately 8000 m³ of LNG as fuel.
Taking the shape of LNG Type C fuel tank one step further,
TGE Marine has recently developed a trilobe Type C tank. The
three cylindrical parts of the tank are arranged horizontally in
transverse direction to the ship’s longitudinal axis. The tank
has been developed with the restrictions of larger container
vessels in mind. Losing only one container bay, a total volume
of 6000 – 8000 m³ can be achieved. A benchmark in
volumetric efficiency has shown that these tanks can achieve
a similar volumetric capacity to membrane type tanks, while
keeping all the benefits of a Type C tank design.
Re-invention of the Type C tank
The development and extension of Type C tanks is not
surprising given the advantages of the Type C tank design
in terms of inherent safety, operational safety and ease of
project execution. Type C tanks are not an ‘old dog’, but can
rather be described as an established technology supporting
newly developed markets, such as the LNG fuel market, with
a long reference list and reducing the risks associated with
the application of new technologies. With new developments
and the adaption of existing technologies to new markets,
the ‘trick’ is to find the right solutions. The developments
in terms of size, shape and arrangement of Type C tanks
can fairly be called a re-invention of this long established
technology.
Figure 4.
Vertical fuel tank arrangement for a 1000 TEU
container vessel.