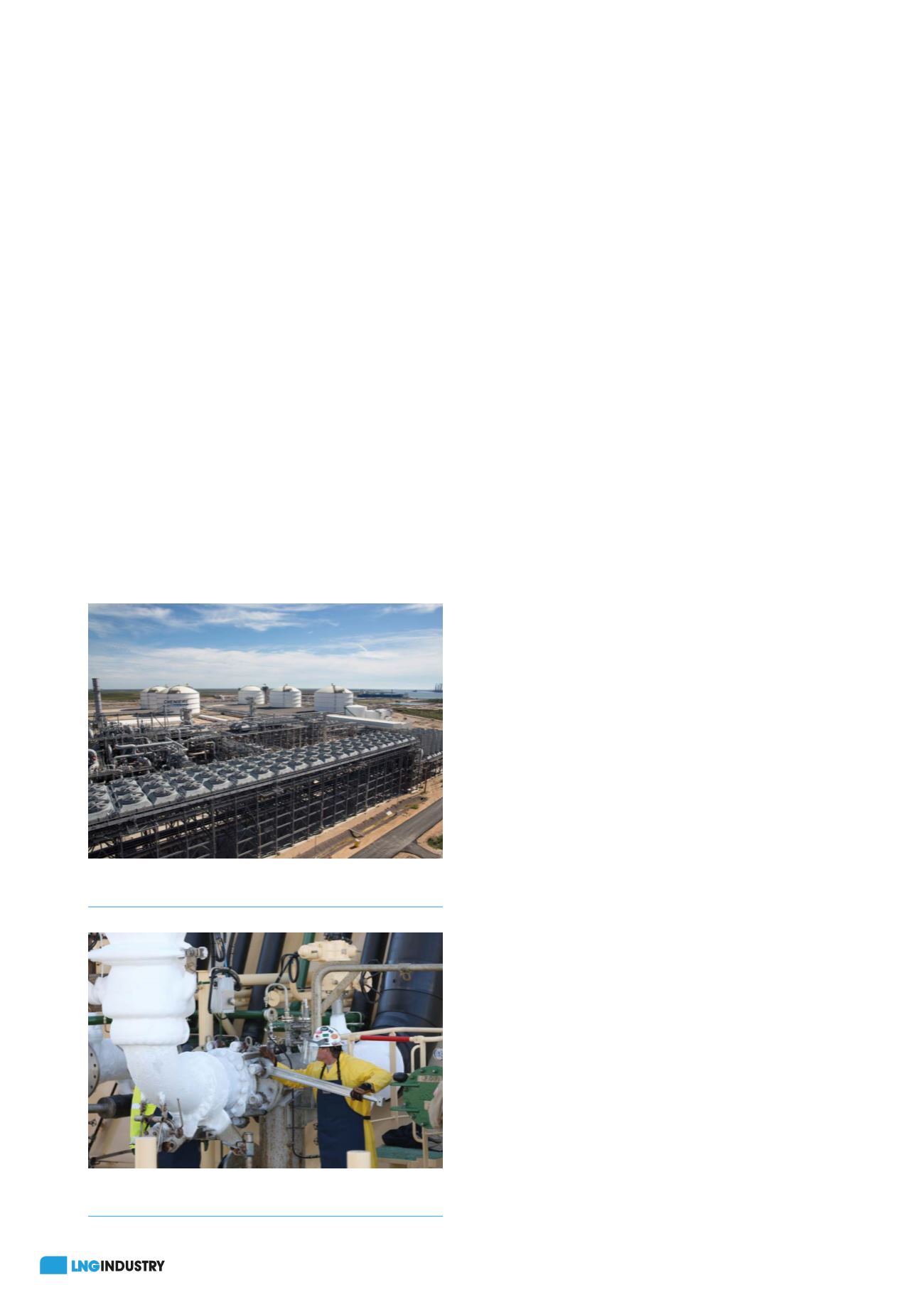
26
January 2020
between maintenance activities. In Cheniere’s case, it is all
done while the company is safely operating the plants for
customers who depend on their LNG being ready.
LNG in the US
With an increased demand around the globe for reliable
and affordable power from a cleaner energy source,
and an abundant supply of natural gas in the US, LNG
offers a practical solution to global energy requirements.
Responding to that demand, numerous LNG projects
have commenced in the last few years, especially in
the US, including the Sabine Pass Liquefaction Project,
Corpus Christi Liquefaction Project, Cameron LNG,
Freeport LNG, Cove Point LNG and Elba Island LNG. Notably,
Cheniere has completed seven trains in seven years, an
average of approximately seven months ahead of schedule.
The next stage for these projects, and indeed for the
industry, is to seek improvements that do three main
things: increase production; reduce emissions intensity; and
preserve reliability. That combination will help push the
LNG industry forward in a global race to provide new
energy.
Being proactive matters
So what is debottlenecking really? Outside of oil and gas
engineers, it is likely that it is not well understood, but it
is also not a completely impenetrable idea either. Think
about it like something we take for granted every day: our
vehicles.
Most of us know that having a well-running automobile
is central to our quality of life. Even a single day of our car
in the shop has costs and consequences we would rather
avoid. We proactively take care of our car to achieve
ongoing optimal performance, better fuel efficiency and
longevity of the engine. It is not enough to just buy a good
vehicle – we commit to maintaining the vehicle and are
proactive now to avoid more cost and increased
inconvenience in the future.
In the LNG industry, debottlenecking can be likened to
being proactive with vehicle maintenance. Debottlenecking
is the process of identifying specific areas or equipment to
optimise performance and increase flow.
And for the real car aficionados, you can take it one
step further, and think about how you turn a regular car
into a championship one. In NASCAR or Formula 1, for
example, everyone knows the drill: you take what you know
about building cars, whether you are Honda, Ford or Ferrari,
and you make the fastest, most efficient, safest racecar you
can. More horsepower, less fuel, more reliable. A real
winner.
By being proactive with train maintenance and
performance, debottlenecking is a bit like turning LNG
trains into Formula 1 trains – they produce more LNG,
while being more efficient, and spend less time offline for
pit stops, or turnarounds as we call them in the industry.
Debottlenecking case study
Cheniere’s version of taking its car in for a tune-up can
now extend intervals between maintenance and reduce the
downtime duration and frequency. In addition to dutifully
bringing in the car in for a tune-up, the company has
gone a step further and adopted a strong proactive and
optimisation principle and engaged in debottlenecking
opportunities.
Cheniere has continuously sought ways to improve
operational performance and reduce its carbon intensity.
The company’s multi-year optimisation and debottlenecking
project to optimise production at its Sabine Pass LNG
facility in Cameron, Louisiana, was announced in late 2018.
Since then, the projects associated with this effort have
resulted in higher plant efficiency and production, while
achieving lower emissions intensity within the plant.
Cheniere employed two approaches to improve facility
optimisation: production and maintenance optimisation,
and debottlenecking projects.
In production and maintenance optimisation, Cheniere
seeks opportunities to extend intervals between
maintenance and reduce the downtime duration and
frequency, all while maintaining reliability and asset
integrity. Using technology and close process monitoring,
the company seeks to maximise operations within the
current plant design, through control system and
procedural enhancements.
With debottlenecking projects, Cheniere evaluates ways
to remove design constraints or bottlenecks and increase
production. Careful plant process modelling and analyses
will identify possible constraints, and Cheniere explores
new technologies that serve to increase performance of
various equipment while reducing demand for fuel or
Figure 2.
One of the trains at Cheniere’s Sabine Pass
liquefaction facility.
Figure 3.
Loading LNG onto a vessel at Cheniere’s
Sabine Pass liquefaction facility.