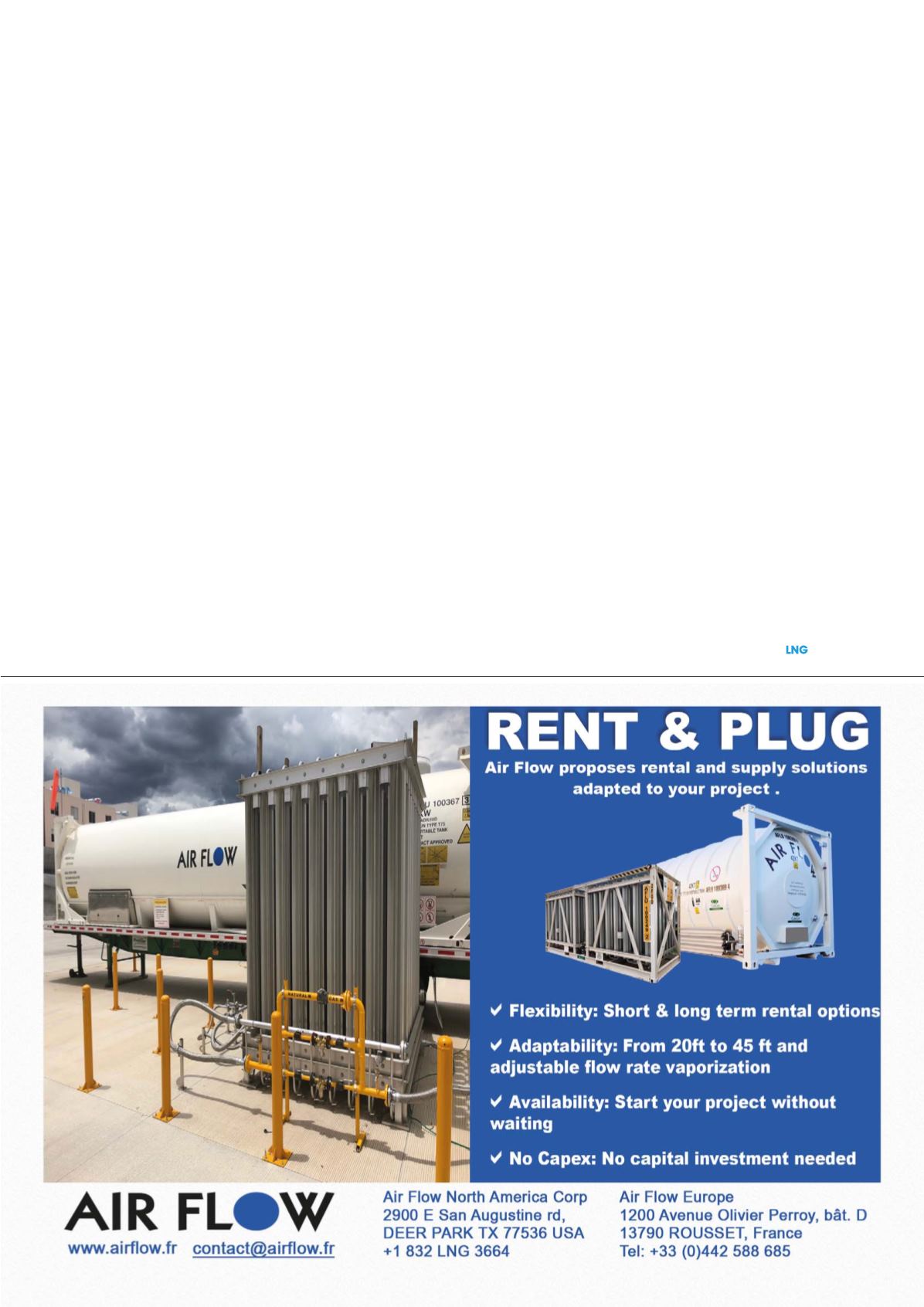
power. The company carefully evaluates all efficiency
opportunities to ensure they are preserving operating
parameters, maintaining plant safety, and adhering to
regulatory requirements.
Debottlenecking and optimisation
realised
In late 2018, Cheniere President and CEO Jack Fusco
announced that the company was raising its run-rate
consolidated adjusted EBITDA and distributable cash flow
guidance. He went on to explain that this announcement
was driven by the increased expected run-rate LNG
production as a result of the significant incremental
production potential identified from debottlenecking
opportunities, maintenance optimisation, and plant
overdesign. Already, the company has raised its run-rate
production guidance to 4.7 million tpy – 5.0 million tpy
per train, up from 4.4 million tpy – 4.9 million tpy per
train.
Debottlenecking also supports the company’s efforts to
reduce the fuel consumption associated with LNG
production and to lower CO
2
emissions intensity arising
from production. Recent debottlenecking activities at the
Sabine Pass facility have yielded a nearly 3% improvement
with regard to fuel consumption and have markedly
reduced CO
2
emissions intensity per unit produced at the
facility.
Increasing production run rates means more LNG to
sell on the same platform. Increasing operational
efficiency means a reduction in emissions intensity.
Imagine what we can do as an industry if we all seek ways
to innovate, optimise and become more efficient
operators.
It is also important to identify the existing plant
constraints before performing any debottlenecking
evaluations. Once existing constraints are identified,
various options to perform debottlenecking projects are
studied. These options might include upgrades or
modifications to, or replacement of, existing equipment.
The debottlenecking approach can be summarised as
follows:
z
Perform debottlenecking study to identify efficiency
opportunities.
z
Scope modifications/upgrades required.
z
Develop and execute action plan with milestones.
Conclusion
When embarking on a debottlenecking and optimisation
project, a company should carefully evaluate all efficiency
opportunities to ensure that it preserves operating
parameters. Plant safety is always the priority and should
be maintained throughout the entire process. Of course, it
is also important that a company continues to adhere to
regulatory requirements.
Underlying a company’s overall operational excellence
program – from extensive planning to execution — is the
notion that a company can and will do better. Taking these
steps to increase efficiencies may not make LNG companies
household names like McDonald’s or Amazon, but it will
create an industry that produces more energy with less
waste, fuelling more households around the world.