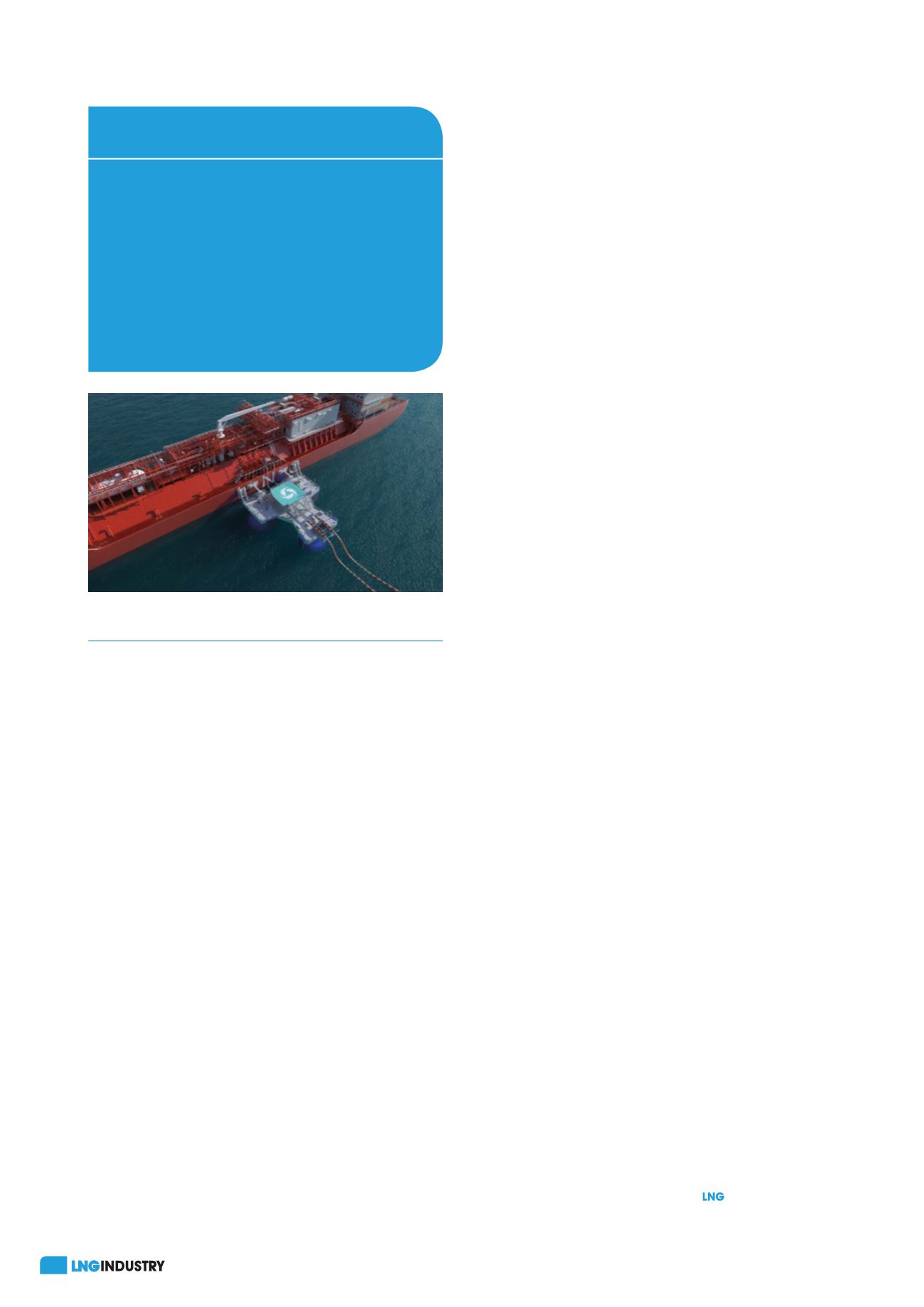
32
January 2020
solution proposed and based on site specific metocean
conditions. The hydrodynamic performance of the system
is confirmed by advanced hydrodynamic models and,
combined with historical metocean data, this predicts the
corresponding uptime at the site. This ensures that the
final design is capable of operating safely and can handle
survival conditions with an associated mooring system.
The goal of this feasibility study is to generate
infrastructure alternatives in order to identify the solution
which offers flexibility to LNG demand, minimal impact to
existing infrastructure, for lowest investment. One of the
existing jetties is deemed as the most appropriate to
modify and accommodate the UTS interface with onshore
piping. The recommended solution is to branch an LNG
line off one of the existing jetties, supported by piles to
the UTS tie-in point. The floating cryogenic flexible pipes
are tied into the rigid pipe above the water and guided
into the water from a simple chute construction. The large
tidal differences at the location is a challenge for a fixed
structure interface to a vessel, so a floating transfer
system like the UTS, which follows the LNG carrier
vertically with the tide, is technically and operationally
advantageous. The transfer system can easily be stored
alongside an existing decommissioned jetty while not in
use.
Case B – small scale LNG for
bunkering
In Case B, both a traditional jetty and a jettyless
alternative are being considered. The aim of this
feasibility study is to generate CAPEX estimates for both
solutions, in addition to analysing how the UTS will
perform from an operational perspective.
Three different locations are analysed, together with
site specific metocean conditions. Consideration is given
to wind and wave conditions, water depth, marine traffic,
operational frequency in the area, tie-in infrastructure
onshore and optimisation of the floating cryogenic hose
length, for both the operation and idle modes of the UTS.
The different locations are weighted in order to conclude
on the optimal mooring location. In general, Case B’s
location shows challenging metocean data, so specific
numerical models are created in order to simulate
resultant hydrodynamic effect on the UTS motion and
mooring system, including the vacuum mooring system
from the UTS to the LNG carrier, for different wave
heights, winds speeds and wave directions. The total
uptime of Case B is dominated by the wave conditions for
the jettyless UTS and is found to be 94%, while the
proposed jetty structure has 92% uptime.
The LNG bunkering market has a sense of urgency due
to the IMO 2020 sulfur cap, so bunkering capabilities along
and around major shipping routes are necessary. In this
Case B, the schedule to build and install a transfer solution
can be considerably compressed, with a UTS lead time of
12 months versus new jetty construction of 36 – 40 months.
The resultant UTS design is well within the design
parameters of the existing UTS unit,
La Santa Maria
.
Consequentially, cost optimisation through product
standardisation ensures a more competitive solution to a
bespoke jetty structure. The study concludes that CAPEX
savings are in the order of 60% for the UTS versus a
traditional jetty.
Conclusions
z
The relative price of small scale LNG compared with
competing fuels is a key factor in determining its
demand in the future, especially in developing and
remote areas.
z
Collaboration across geopolitical boundaries is
required. Proactive participation from regional
stakeholders on policies, regulations and permits will
simplify and incubate innovation and investment.
z
Small scale LNG Infrastructure needs to modularised.
Bespoke civil works with specialised labour force is
costly and time-consuming. Standard plug-and-play
solutions will reduce the CAPEX burden, as well as
minimising project execution risk, cost and schedule
overruns.
z
The two cases illustrated here are common across
the globe. It has been proven that jettyless versus
traditional jetty construction answers the global
climate challenge.
z
In addition to being highly cost-effective and
providing significant schedule reductions, the floating
UTS is easily transportable to solve the next energy
challenge, thus answering the needs of spot markets
and fluctuation in energy needs.
Innovation highlight: UTS
vacuummooring system
The UTS’s mooring system is a vacuum-based automated
mooring technology that safely holds even the largest
450 000 DWT bulk vessels and Super Post-Panamax
container vessels. It eliminates the need for conventional
mooring lines. Remote controlled vacuum pads attached
to hydraulic actuated arms extend, attach and moor ships
in a few seconds.
Such systems have successfully completed more than
500 000 automated mooring operations and, by 2020,
approximately 500 000 such operations will be made
annually.
Figure 4.
Simple and field proven vacuum attachment
system accommodates any size carrier.